Transforming infrastructure to improve efficiency
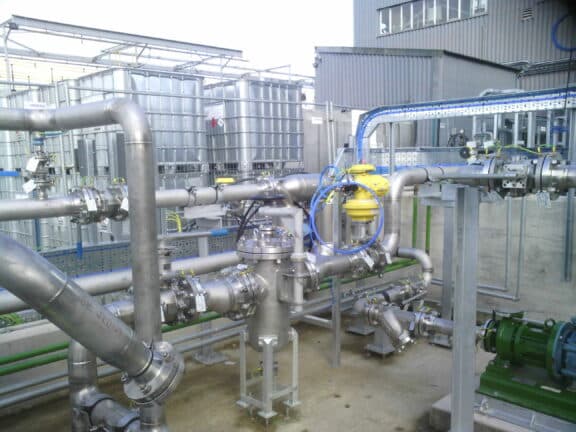
Services provided
Client Requirements
Our client manufacture and market paints, coatings and associated products. It supplies stains, equipment and floor covering products, architectural paints, coatings, and varnishes. The company sells its products to professional, industrial, retail and commercial customers.
With the goal of bolstering their epoxy resin production capabilities the client, required their existing facility completely transformed removing existing outdated equipment and upgrading their existing systems, equipment and pipework.
To meet this ambitious objective, BGEN were appointed as the Principal Contractor, assigned to deliver mechanical, electrical, instrumentation, and installation services, including fabrication and supply of all steelwork and pipework.
Our Solution
In response to the clients’ critical requirements, BGEN, implemented a comprehensive solution that seamlessly integrated various components into the facility. This solution was meticulously crafted to address the specific operational and safety challenges while optimising space and ensuring structural enhancements.
To accommodate the new vessels and tank the existing equipment needed to be removed and new elements needed to be constructed and skilfully modified. This included the erection of new stanchions, columns, and frames to offer structural integrity. To optimise the space a mezzanine, secondary platform, and access staircases were all installed ensuring efficient utilisation of the available space for housing the vessels and tanks, as a result effectively increasing operational capacity. They were complimented by insulation measures to improve energy efficiency and ensure product containment in case of unforeseen incidents.
Over 100 items were installed including vessels, pumps and filters supported by a remarkable 30,000 meters of electrical and control cables, 32,000 meters of instrumentation cables, deployment of 6,650 meters of stainless steel and carbon steel, and 350 meters of Galvanized steel. All are complimented by fabrication, galvanization, and installation of an impressive 5,656 pipe supports. Improving operational, production and energy efficiency for the client.
BGEN executed each phase of the project with precision, encompassing mechanical and electrical works and structural enhancements, ensuring a seamless and efficient execution whilst maintaining safety and compliance with industry standards and stringent safety regulations. Now the client benefits from a state-of-the-art facility fully compliant to support the production of epoxy resin.
Client Benefits:
A single point of contact: To manage the project from start to finish and ensure it’s delivered on time and to the design specification.
Improved facility: The upgraded facility improves safety for both products and personnel and provides streamlined processes and increased productivity, effectively addressing the operational requirements of the client.
Space optimisation: The creation of mezzanines, secondary platforms, and access staircases optimised the facility’s use of space, seamlessly accommodating new vessels and tanks.
Energy Efficiency: The cladding and insulation measures contributed to improved energy efficiency, ensuring cost-effective operations.
Structural Integrity: The new stanchions, columns, and frames ensured the structural integrity of the extension, meeting the demands of the epoxy resin production train.
BGEN’s transformative, all-encompassing solution exemplifies our commitment to delivering comprehensive, quality-driven, and safety-focused services. The partnership with BGEN has empowered the client with a modernised, efficient, and safe facility, fully equipped to cater to the dynamic demands of a growing industry. This project symbolises the effectiveness of integrated solutions in achieving success in industrial expansions.